Solution for the EnQuest Magnus Platform
EnQuest Magnus (formerly BP Magnus) was one of BP's best-known assets on the UK continental shelf and BP has benefited from a long production run from the oil field. As well as providing hydrocarbon production from the field, Magnus is also the entry point for the Northern Leg gas pipeline, with gas exports from other nearby installations feeding the network for transfer to the onshore St Fergus gas terminal via Brent's.
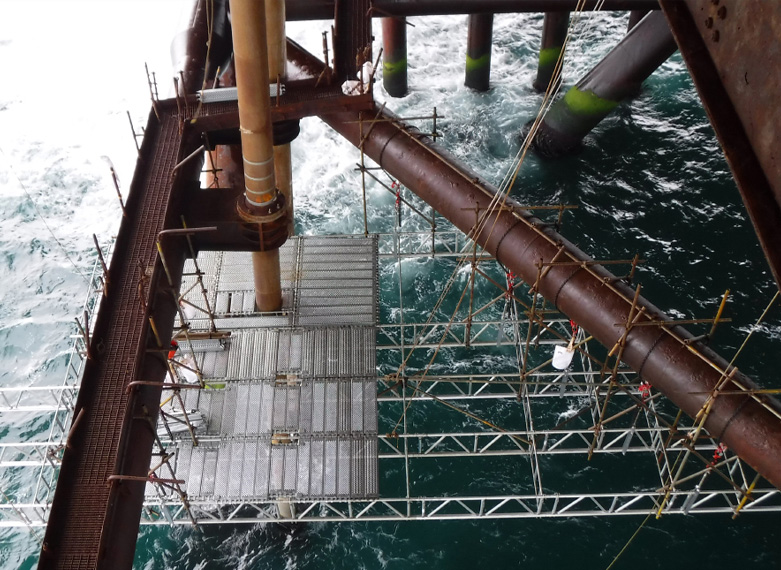
The scope of the work
One of the support structures on the Northern Leg's riser had failed, and even if the pipeline continued to be used, another similar incident would require the pipeline to be shut down, resulting in significant financial losses for many operators. An earlier attempt to construct a traditional stand for accessibility at the site had failed due to the long installation time and subsequent risk of contact with the ocean waves.
Cape PLC, after the failed attempt at traditional scaffolding, engaged HAKI Access Solutions to design, engineer and install a suitable access solution for the repair work.
The main requirement for the project was quick installation as it was mainly the long installation time and the risk of damage to the scaffold structure due to high waves which had been the problem when, in the previous attempt, access for repairs was to be made at the site in question.
Best solution
HAKI Access Solutions (now part of the HAKI Group) proposed the use of HAKISPAN's suspended platform and enabled access for the customer with a suspended staircase. This system, developed in collaboration with HAKI, was considered the best option as it offered the shortest installation time with sufficient capacity for the required scope of work. For the solution, they used the suspension components of Span's own TechniSpan, which they integrated completely into HAKI's system.
Our team made their way to Magnus and dismantled the remainder of the wave-damaged scaffolding using special ropes before installing the platform.
In the next step, an environment was constructed that would allow welding work to be carried out on the platform so that the new steel structure could be lifted into the correct position and hot work could be carried out under safe conditions. All repairs were carried out with a distance of only 9 meters to the sea surface.
Project results:
- The solution was fully installed over 21 days with 14 productive shifts available to our team.
- The process was documented on site with continuous reports to the mainland for coordination. In this way, it was possible to minimise the number of stops for checks of the current stage of the installation.
- All the work could be done inside with minimal impact from prevailing weather conditions and could be completed while it was still summer weather. This allowed the Northern Leg gas pipeline to remain operational throughout the repair work, bringing significant financial benefits to all those dependent on its operation.
- Thanks to the successful repair, the transfer of ownership from BP to EnQuest was smooth.